Strategic framework and innovative thinking earned Port Tanjung Pelepas the CIPS Procurement Team of the Year
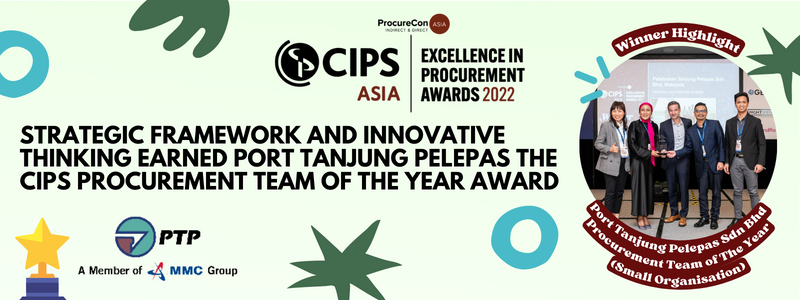
Port Tanjung Pelepas Sdn Bhd winner of the Procurement Team of the Year award in 2022!
The Procurement Team of the Year award is given to a procurement team who have made a significant and outstanding improvement to their performance and culture which has led to increased effectiveness, influence, efficiencies, savings and competitive advantage. The winner has impressed judges with their contribution to the business as a whole, and the team’s diligence, commitment and perseverance to continuous improvement.
The Supply Chain Division at Port Tanjung Pelepas Sdn Bhd knew they wanted to reduce costs and make a dent in the inventory reduction for the business. The team embarked upon the project ‘Inventory Cost Reduction Strategy for Stock Optimisation’ which addressed vital areas that had been identified for improvement before implementing a series of changes that tackled the organisational needs from a ‘bird’s eye view’ perspective resulting in reduced inventory holding by 33% from Q4 2019 and reduced slow moving stock by 35% from Q4 2020.
The key objectives they set out were:
- Optimisation of spare part purchasing
- Spare part cost saving
- Achieving stock availability
- Reducing inventory holding cost
- Minimising the risk of holding ageing stock
- SKU harmonisation
- Storage space optimisation
- Improvement of service level to internal and external stakeholders
After an in-depth assessment of the business needs, involving brainstorming activities, reviewing existing processes to identify the gaps, Kaizen programs, performing market outreach and analysis from various industries and accredited global standards sources. Port Tanjung Pelepas Sdn Bhd identified the main concerns they wished to tackle. They set up a ‘Transformation of Procurement and Inventory Team’ made from existing Procurement-Direct Material Commodity, Parts Management and Warehouse team from the Engineering Division who aimed to improve spare parts inventory, supply ability and mitigate the supply disruption.
Watch: CIPS Asia Excellence in Procurement Awards 2022: Port Tanjung Pelepas - Procurement Team of the Year
Following this assessment, Port Tanjung Pelepas Sdn Bhd implemented:
- New inventory strategies were developed and implemented by optimising spare parts purchasing, improving on demand management by performing inventory data analysis, and part categorisation was developed to identify fast and slow-moving spare parts associated with inventory cost.
- Results: Significant inventory reduction and improvement to supply ability which reduced by 33% from Q4 2019 – Q4 2021. There was a 35% reduction in slow-moving stock in Q4 2020
- Acquisition management by embedding a contract management strategy to reduce inventory holding, reduce transportation costs and reduce risk due to urgency. Better inventory control to avoid the excessive stock, purchase at the right time and quantity to reduce stock-outs.
- Results: Sold excess spare parts - inventory value was reduced by 11% from Q4 2020 to Q4 2021. PTP’s suppliers manage to reduce their maintenance costs by buying PTP’s excess spare parts.
- SKU harmonisation of spare parts master data: cleaning and standardising data, matching data from all the sources to consolidate duplicate items.
- Results: Identified duplication of items, and made a reduction from 28,000++ SKUs to 16,000+. Managed aged and obsolete spare parts and adjusted demand forecasting based on ABC-XYZ analysis.
- The reduction of ‘out-of-stock inventory items: with the implementation of reorder level and Safety Stock strategies.
- Results: Identified the right time and quantity for when the stock needs to be replenished. Engineering implemented an effective plan for their maintenance program supporting equipment availability to Operations.
Top 10 Key Learnings:
- Collaboration and teamwork are vital in getting the right input and successful outcomes.
- Successful improvements require process changes to be adopted by the whole team.
- Adopt a systematic framework to process changes as a guide for the team.
- Close the process gaps across divisions.
- Enable the supply chain to improve service levels for internal stakeholders.
- Adopt a successful process for inventory management.
- Give the team opportunities to improve their skills.
- Involve the internal team, customers and suppliers in the transformation journey.
- Increase the confidence level of internal and external customers.
- The correct requirement given to the suppliers enables them to make early preparation for the supply and maintain the price offer despite market volatility.
One of the biggest challenges Port Tanjung Pelepas Sdn Bhd faced was surrounding data – a common challenge across the board during a digital transformation journey. They struggled to gain data from the respective divisions and departments which lead to gaps and inconsistent data.
The inaccuracy of item specifications in the master data was also a big problem, as it is for many. The same products have multiple items code created due to insufficient specification which led to issues when tracing equivalent item codes during replenishment which may have caused the wrong items to be purchased.
What impressed the judges the most was the collaboration and teamwork in achieving their goals and their effective strategy concerning the harmonisation of data. Port Tanjung Pelepas Sdn Bhd proved that successful improvements required a team effort, spanning the whole business and ‘out of the box' thinking to implement changes that made a real difference. Different team members came forward with suggestions on how to improve processes and key stakeholders backed the transformation - everyone came together to achieve results.